Automatic pellet boiler
(complete device with burner, built-in hopper and pellet conveyor)
- Pellet heating
- Instalation
- Boilers regulation
- Refuelling
- Boiler cleaning
- Technical details
- The pellet burner
- Downloads
-
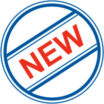
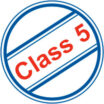
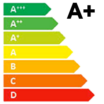
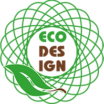
The boilers are designed for electronically controlled pellet combustion with automatic fuel ignition. The pellet burner is built into the front part of the boiler in the door of the lower combustion chamber. This chamber is lined with ceramic fittings for ideal flame burning with high efficiency and also serves as space for ash. In the rear part of the boiler there is a tube heat exchanger equipped with segment brakes with the function of rough (operational) cleaning without the need to remove them.
The boiler body is made as a weldment from steel sheets with a thickness of 3 – 5 mm. Externally thermally insulated with mineral felt and sibral insulation, inserted under the sheet metal covers of the outer casing of the boilers. In the upper part there is a fuel tank, from which the pellets are transported to the burner by means of a screw conveyor. Fuel metering is controlled completely automatically. In front of the boilers there is a panel with the main switch, pellet burner switch (L2) for cleaning, operating (boiler control) thermostat, safety thermostat, thermometer and 6.3 A fuse. DxxPX boilers are equipped with an exhaust fan (except D10PX). The boiler isn’t equipped with a cooling loop against overheating, because due to the small amount of fuel in the burner, there is no danger of the boiler overheating in case of blackout.
Advantages of special compact ATMOS boilers of new design
- Compact dimensions for small boiler rooms
- All in one – boiler and pellet hopper, conveyor and burner
- Large ceramic combustion chamber
- Exhaust fan – (except D10PX)
- Tubular heat exchanger with the possibility of operational cleaning
- High efficiency over 90 %
- Great heating comfort – fully automatic boiler operation
- Convenient ash removal – easy cleaning only from the front
- Small size and low weight
- Possibility of equipping the boiler with pneumatic transport of pellets
- Possibility of fitting the burner with pneumatic cleaning
- Ecological combustion – boilers according to EN 303-5:2012 class 5, EKODESIGN 2015/1189
Pellet heating
Most of us already have some experience in using with wood or wood briquettes, either in boilers or fireplaces. These fuels are available in most places at more or less decent prices. A novelty, that not everyone knows, are the so-called pellets, which are produced in a similar way as wood briquettes, by pressing from waste wood (dry sawdust and shavings) without any binder under high pressure. We consider quality pellets to be pellets made only of soft wood without bark, so-called white pellets, which will guarantee us trouble-free and reliable boiler operation. Today, however, there are manufacturers who add biological binders to pellets for greater strength, especially for pneumatic transport. These pellets can be burned, but it is necessary to take into account the greater ash content and non-burning.
Pellets can be produced by the same way from hard wood or wood with bark so called dark pellets but these can cake in the burning chamber and can cause troubles. It is possible to burn these pellets in our burners, but it is necessary to clean the combustion chamber of the burner once a day. When burning quality pellets without binders and bark, we clean the combustion chamber of the burner once every 7 and 30 days. Similar or even greater problems occur when burning straw pellets and various biological wastes, such as poppy seeds, sugar beet pulp, grain waste, etc. These pellets contain high amounts of chlorine and nitrogen, thus sharply shortening the life of the boiler body, ceramics and chimney. Therefore, we cannot recommend burning them. The most common size of quality wood pellets today is a diameter of 6 and 8 mm and a length of 10 to 25 mm. The calorific value of pellets is approximately from 16 to 19 MJ / kg depending on the type of fuel. Today, the price of quality pellets ranges from producers, of which there are already many in the Czech Republic from 5,000 to 7,000 CZK per tonne.
So far, pellets in the Czech Republic are most often delivered in plastic bags of 15 kg each, or in bales of 1000 kg. Abroad, but now also in the Czech Republic, the pellets are transported by means of tanks from which you can refuel in any tank, just like with LTO. However, it is necessary to follow several principles that prevent their crushing during pneumatic transport. Above all, it is necessary to prevent them from falling directly on the hard wall of the container, but on the curtain, which is suspended in the middle of the container from the ceiling. This will ensure even filling of the hopper and prevent them from being crushed into small pellets and dust. However, it is important that the pellets are stored in a dry place so that they do not disintegrate.
- Control panel and connecting hose from the conveyor
- Open pellet hopper with a volume of 65 l / 175 l / 215 l
- Open combustion chamber with burner
- Combustion chamber with ceramic fittings
- Exhaust fan (except D10PX) and flue
Instalation
The prescribed solution consists in the installation of the boiler with Laddomat 22, or a thermoregulation valve, which allows you to create a separated boiler and heating (primary and secondary) circuit to ensure the minimum temperature of return water to the boiler of 65 °C. The higher the return water temperature is, the lower you will keep condensation of tar and acids that are harmful for the boiler body.
We keep the outlet temperature of the boiler in the range of 80 – 90 °C and set the temperature of the water to the radiators or floor heating on the mixing three-way valve as needed (e.g. 30 – 80 °C).
Another variant is connection of the boiler with a three-way mixing valve with an actuator controlled from the electronic controler (e.g. ACD 03, ACD 04) to keep minimum temperature of the water returning to the boiler (65 – 75 °C).
We recommend you to always connect the D10PX, D15PX, D20PX and D25PX boilers with an buffer tank with the volume of 500 to 1000 l. When connecting the boiler with the buffer (accumulation) tank, the boiler is controlled best according two TS and TV sensors located on the tank. To control the burner according two temperatures on the buffer (accumulation) tank it is necesary to place two KTF 20 sensors (TV and TS sensors) on this tank.
- Laddomat 22
- Connection of DxxPX boiler with buffer tank
- Connection of DxxPX boiler with buffer tank and ACD03 control
- Possible connection of the DxxPX boiler without buffer tank and control of the boiler pump according to the boiler temperature (TK sensor) from the A25 burner
- Connection of DxxPX boiler with expansion tank for burner regulation according to TS and TV sensor and boiler pump control according to boiler temperature (TK sensor) from burner A25
Boilers regulation
The boilers are supplied to consumers with the basic control output of the boiler, which meets the requirements for heating comfort and safety. The regulation ensures the required initial temperature of the boiler water (80 – 90 °C). The boilers are insulated with a connector for connecting pumps in the boiler circuit and functions for its control directly from the ATMOS A25 burner control.
DxxPX boilers are factory-fitted with TK boiler temperature and TSV flue gas temperature sensors. TK sensor inserted in the boiler sump, TSV flue gas sensor built into the boiler flue, all together connected directly to the burner connector. The ATMOS A25 pellet burner directly controls the boiler exhaust fan (reserve R) and the pump in the boiler circuit (reserve R2). Output R2 is factory-fitted with a thermostat for the pump in the TC70 °C boiler circuit.
With the recommended connection of the boiler with a buffer tank, the boiler is best controlled according to two TS and TV sensors located on the tank. Switching of pumps in the system circuit in this case is not dependent on the boiler temperature, therefore it is solved according to the potential needs of the system.
- Boiler control panel with standard regulation
Panel composition:
Main switch, safety thermostat, thermometer, control thermostat and flue gas thermostat
Electromechanical control is the optimal solution for controlling the operation of the boiler (fan) in a simple way.
The design of the panel with standard regulation is the basic design for all manufactured boilers.
Equithermal regulation ACD 03
Each boiler can be equipped with a modern touch electronic control ATMOS ACD 03 for controlling the entire heating system depending on the outdoor temperature, room temperature and time. This regulation is able to control the boiler itself with a fan with many other functions.
- Boiler control panel with equithermal regulation ATMOS ACD03
Refuelling
The boiler is equipped with an integrated fuel reservior that must be refilled in the interval from 1 to 3 days.
If the alarm message ALARM PELLETS – REFILL PELLETS appears on the burner display, pellets must be added to the fuel tank. Open the tank cover in the top part of the boiler and add pellets. When the pellets are added, it is not necessary to pump the pellets to the conveyor! The boiler is equipped with a special function against its full emptying.
In the case that the refueling interval is too short for your needs, there is an option to extend the pellet resevoir. Extensions can be folded together. It is, however, necessary to buy additional compact stepstool for convenient refueling according to all valid safety regulations.
However, additional buying of the pneumatic pellet feeder ATMOS APS 150 SPX (D10PX) / ATMOS APS 250 SPX (D15PX and D20PX) / ATMOS APS 250 SPX2 (D25PX) for convenient automatic refueling from any silo, eg, for the whole season (textile silo, separate room), is the ideal solution.
- Example of standard refilling of pellets from 15 kg bags
- Boiler with pneumatic transport of pellets ATMOS APS 250 SPX (2)
- Reservoir extensions for DxxPX boilers
- DxxPX boiler with 300 mm reservoir extension
- Boiler room with DxxPX boiler and storage tank with multipoint suction of pellets by pneumatic conveying ATMOS APS 250 SPX (2)
Boiler cleaning
The burner and the boiler must be cleaned regularly and thoroughly once every 5 to 14 days depending on the quality of pellets and the output setting.
The boilers are able to burn only good quality white pellets from soft wood without bark ø 6 – 8 mm, lenght 10 – 25 mm with heating power 16 – 19 MJ.kg-1. Boilers are not able to burn pellets with high sintering in the burning chamber of the burner. In such case it is needed to clean the burning chamber once a day. The pellet burner ATMOS A25 can be equipped with pneumatic cleaning of the combustion chamber. It will be appreciated especially by those using lower quality pellets.
Comfortable ash removing – easy cleaning only from the front. Remove the ash from the whole cleaning chamber with the half-round ash pan (accessory of the boiler). Insert the ash pan into the boiler to the end, push the ash into the ashtray by thrusting it into the rear wall and remove the ashtray. Never leave the ash pan in the boiler!
DxxPX boilers are equpied with function of operation cleaning of the tube exchanger. Use the handle on the cleaning lid in the rear part of the boiler hidden under the cover for operation cleaning of the tube exchanger and decelerators. By repeated pulling out and releasing of the handle the ash is knocked out from the decelerators and the tube plate walls are scraped off.
- Example of ash collection using an ashtray
- Demonstration of operational cleaning of a tube heat exchanger
Technical details
Description of the boiler drawing | |||
1. | Boiler body | 16. | Main switch (red) |
2. | Cleaning door | 17. | Control (boiler) thermostat |
3. | Pellet burner ATMOS A25 | 18. | Burner switch (black) |
4. | Control panel | 19. | Safety thermostat |
5. | Conveyor | 20. | Fuse T6,3A/1500 -H type |
6. | Door filling – Sibral – large with the hole for burner | 21. | Cleaning lid cover |
7. | Door seal – cord 18 x 18 mm | 22. | Exhaust fan (except D10PX) |
8. | Closure | 23. | Condenser for exhaust fan – 1μF |
9. | Insulation under the burner | 24. | Cleaning lid of the rear drain |
10. | Fuel reservior 65 l (D10PX) / 175 l (D15PX, D20PX) / 215 l (D25PX) | 25. | Reservoir cover |
11. | Tube heat exchanger | 26. | Burner connecting hose – Ø 65 mm – length 550 m (D15PX, D20PX, D25PX) – length 480 m (D10PX) |
12. | The decelerator with a cleaning pull rod and handle | K | – flue gas neck |
13. | Heat-resistant fitting – bottom of the combustion chamber + rear part for D10PX | L | – water outlet from the boiler |
14. | Heat-resistant fitting – shield | M | – water inlet to the boiler |
15. | Thermometer | N | – socket for the filling tap |
Boiler dimensions (mm) |
Boiler type |
|||
D10PX | D15PX | D20PX | D25PX | |
A | 1221 | 1411 | 1411 | 1411 |
B1 | 995 | 1145 | 1145 | 1345 |
B2 | 1150 | 1447 | 1447 | 1647 |
C | 594 | 674 | 674 | 674 |
D | 1012 | 1213 | 1213 | 1213 |
E | 128/130 | 150/152 | 150/152 | 150/152 |
G | 140 | 140 | 140 | 140 |
H | 950 | 1150 | 1150 | 1150 |
CH | 166 | 166 | 166 | 166 |
I | 180 | 180 | 180 | 180 |
J | 6/4″ | 6/4” | 6/4” | 6/4” |
Specifications | Boiler type | ||||
D10PX | D15PX | D20PX | D25PX | ||
Rated power | kW | 3 – 10 | 4,5 – 15 | 4,5 – 20 | 4,5 – 24 |
Heating surface | m2 | 1,5 | 1,9 | 1,9 | 2,2 |
Fuel shaft volume (reservoir) | dm3 (l) | 65 | 175 | 175 | 215 |
Feeding hole dimensions | mm | 542 x 480 | 542 x 480 | 542 x 480 | 542 x 480 |
Prescripted chimney draft | Pa/mbar | 13 / 0,13 | 15 / 0,15 | 16 / 0,16 | 17 / 0,17 |
Max. working overpressure of water | kPa/bar | 250 / 2,5 | 250 / 2,5 | 250 / 2,5 | 250 / 2,5 |
Boiler weight | kg | 287 | 345 | 345 | 418 |
Gas-outlet pipe diameter | mm | 128/130 | 150/152 | 150/152 | 150/152 |
Ingress protection | IP | 20 | |||
Electric input – at startup – during operation |
W | 522/1042 42 |
572/1092 92 |
572/1092 92 |
572/1092 92 |
Efficiency over the entire performance range | % | 91,6 | 92,7 | 91,5 | 91,8 |
Boiler class | 5 | 5 | 5 | 5 | |
Energy efficiency class | A+ | A+ | A+ | A+ | |
Flue gas temperature at nominal output | °C | 117 | 118 | 142 | 145 |
Waste gas combustion products flow weight at nominal output | kg/s | 0,008 | 0,011 | 0,015 | 0,018 |
Specified fuel (preffered) | quality pellets with a diameter of 6 – 8 mm with a calorific value of 16 – 19 MJ.kg-1 | ||||
Average fuel (pellets) consumption at nominal output | kg.h-1 | 2,3 | 3,6 | 4,5 | 5,4 |
The volume of water in the boiler | l | 50 | 76 | 76 | 85 |
Boiler hydraulic loss | mbar | 0,19 | 0,20 | 0,20 | 0,22 |
Minimum buffer tank volume | l | 300 | 500 | 500 | 500 |
Connecting voltage | V/Hz | 230/50 |
The prescribed minimum return water temperature in operation is 65 °C.
The prescribed operating temperature of the boiler is 80 – 90 °C.
The pellet burner
Pellet burner ATMOS A25 for boilers D10PX, D15PX, D20PX and D25PX
Specified fuel: good quality pellets with 6 – 8 mm diameter, 5 – 25 mm lenght and 16 – 19 MJ.kg-1 caloric power (white pellets).
The burner screen: used to display the current status of the burner and adjusting its functions.
Burner control: with an AC07X electronic control unit that controls the operation of the external conveyor, two ignition spirals and the fan in accordance with requirements of the boiler and the heating system. The electronic system is rotected with the safety thermostat of the boiler, safety thermostat at the pellet supply to the burner, the fan speed transducer and the flame sensing photocell. The operation of the burner is indicated on the electronic control display.
Burner in version for boilers DxxPX contains moreover additional module AC07X-C – (R5, R6) to controle pneumatic cleaning system for pellet burner or other possible aplications.
Fuel ignition: automatic by two electric ignition spirals (one ignition spiral 522W).
Basic functions of burner:
Spare outputs R and R2 for control of exhaust fan of the boiler and pump in the boiler circuit (connected from the production)
The possibility of using two spare outputs R5 and R6 for various applications
The possibility of the involvement of four different sensors TS, TV, TK and TSV
TK – boiler temperature sensor (connected from the production)
TSV – flue gas temperature sensor (connected from the production)
TS – temperature sensor on the tank bottom
TV – temperature sensor on the tank top
- control of boiler fan from burner with the help of the spare output (R- reserve) (connected from the production) (except D10PX)
- control of boiler pump from burner with the help of the spare output (R2- reserve) (connected from the production)
- burner controlling it in accordance with two temperatures (sensors) on the buffer (accumulation) tank
Fuel feeding: for boilers DxxPX is designed special auger conveyor DRA25 which is inbuilded directly inf the boiler. This conveyor is controlled from electronic regulation of burner and dose the fuel from the reservoir in to the burner.